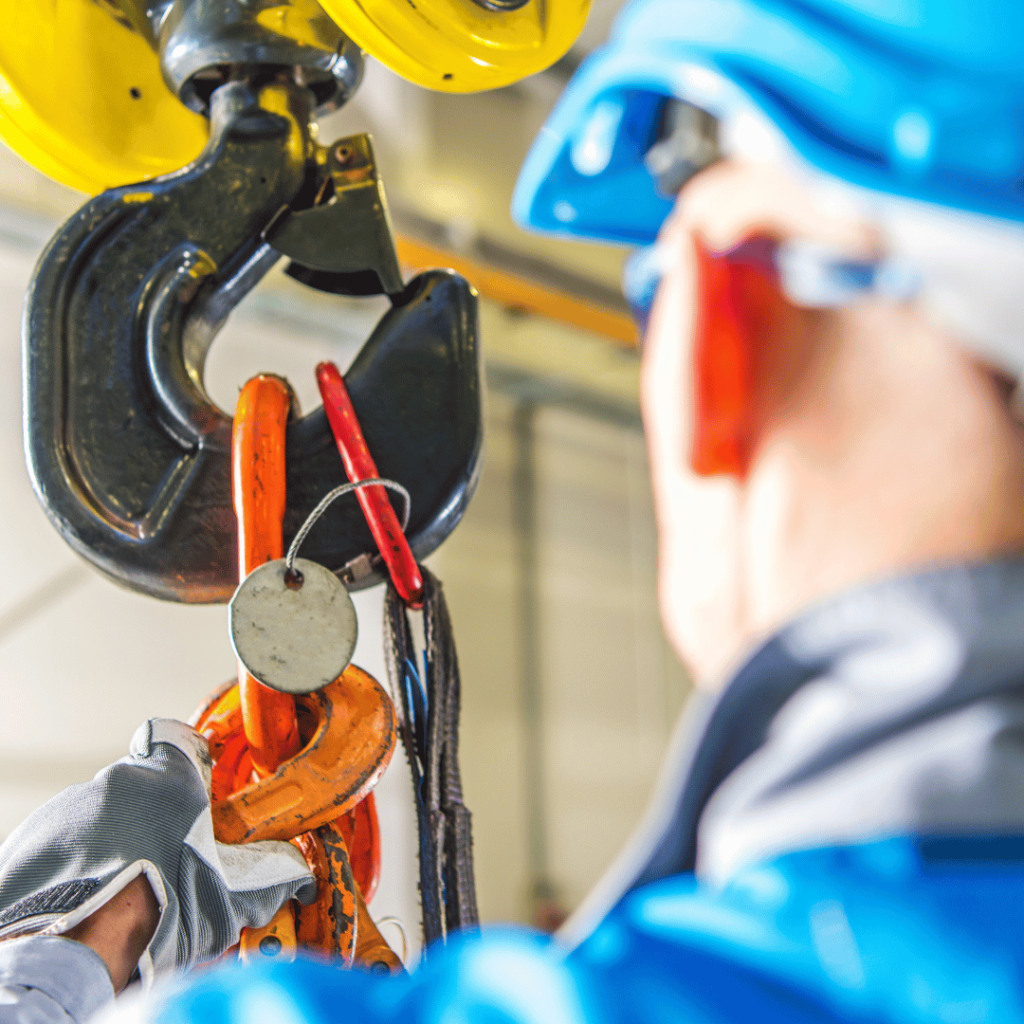
了解工作场所的安全起重操作
在本课程中,您将学习:
- 介绍安全起重作业,概述范围、目的和监管要求,以确保符合安全标准。
- 影响安全起重作业的因素,包括机器功能、材料特性、环境条件、人为因素和起重方法。
- 起重作业中风险评估和工作许可制度的重要性,以及在发生变化时如何调整的指南。
- 选择适合起重作业的设备时要考虑的关键因素是确保起重设备的正确定位、安装和识别。
- 确保安全使用具有可变安全工作负荷 (SWL) 的设备,并进行使用前检查以维护安全并防止事故。
- 参与起重作业的人员(包括承包商和起重团队)以及负责起重设备安装和维护的人员的角色和职责。
- 起重作业的紧急响应程序和应急计划,确保在发生事故时能够有效应对。
- 制定起重计划,强调其重要性、所有权、用途和影响它的因素,并确保与风险评估和工作许可制度保持一致。
- 了解何时以及如何改变起重计划以适应不断变化的条件或新信息。