In many high-risk industries safety isn’t just something to think about—it’s the heart of every operation. Every day, workers face risks ranging from falls and equipment failures to chemical exposure. That’s why proactive safety measures are not just important; they’re vital. And one of the simplest but most effective tools for preventing accidents is the Toolbox Meeting.
If you’ve worked on a job site, you’ve probably attended one of these quick, focused gatherings. But if you’re new to the concept, a toolbox meeting is a brief safety discussion that happens right before work starts. Despite their simplicity, these meetings can significantly reduce accidents, improve compliance with safety regulations, and create a stronger, safety-focused culture across industries.
What is Toolbox Meeting?
A Toolbox Meeting (or “toolbox talk”) is a short, informal gathering where the day’s safety concerns are addressed before work kicks off. These meetings usually last around 10 to 15 minutes and focus on specific hazards or tasks that are about to be tackled. The goal is to keep safety fresh in everyone’s mind.
Toolbox talks are not about overwhelming workers with information. Instead, they’re short and to the point, led by a supervisor or safety officer. Topics can range from how to correctly wear personal protective equipment (PPE) to discussing any hazards workers should watch out for during the day’s tasks. It’s an easy, quick way to ensure everyone stays informed.
Why Toolbox Meeting Matter, Especially in High-Risk Jobs
Whether you’re in construction, manufacturing, or marine industries, toolbox meetings are vital. These environments are full of potential hazards—heavy machinery, heights, chemicals—and the more aware workers are, the safer they’ll be.
But the importance of toolbox meetings goes beyond simply preventing accidents. Here’s why they’re crucial:
- Reducing Accidents: Toolbox meetings keep safety top of mind, preventing injuries by reminding workers of the proper protocols.
- Staying Compliant: Regulators like OSHA (Occupational Safety and Health Administration) or MOM (Ministry of Manpower) often require regular safety talks. These meetings help you check that box.
- Fostering a Safety-First Mindset: When toolbox meetings happen regularly, they reinforce that safety isn’t just a policy—it’s a culture. Workers who feel that their safety is a priority are more likely to follow the rules and stay vigilant.
- Saving Money: Safety incidents don’t just hurt people—they hurt businesses, too. They lead to delays, compensation claims, and even fines. Toolbox meetings can help you avoid these costly disruptions.
- Continuous Learning: Safety isn’t a one-time event. Toolbox meetings are a great way to continuously learn from past experiences, improving safety protocols along the way.
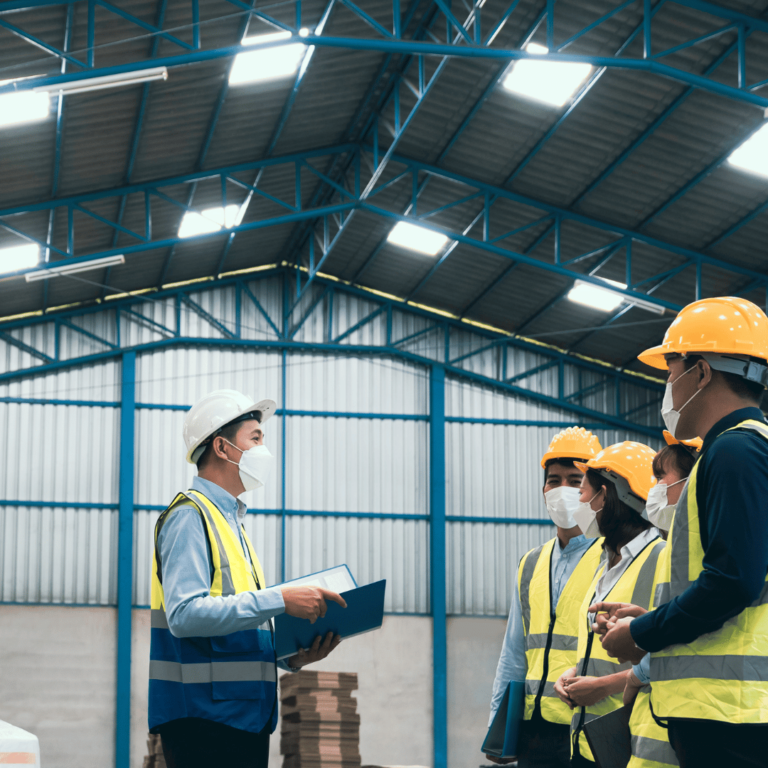
How to Run a Toolbox Meeting That Makes an Impact
Now, while toolbox meetings seem simple, running an effective one takes some thought. To keep things engaging and make sure the information sticks, it’s important to plan and deliver them well. Here’s how:
1. Pick Relevant Topics for the Day
Make sure each meeting is laser-focused on the work happening that day. If the team is working at heights, talk about fall prevention. If hazardous chemicals are involved, discuss safe handling techniques. Tailoring the meeting to daily tasks keeps it relevant.
Here are some common topics:
- Safe lifting practices
- PPE (Personal Protective Equipment) usage
- Confined space entry procedures
- Hazardous material handling
- Emergency response plans
2. Get Everyone Involved
Toolbox meetings shouldn’t be one-sided lectures. Encourage workers to ask questions and share their experiences. You never know—someone might point out a hazard you didn’t even think about.
Real-world insights are valuable, and when everyone feels involved, the meeting becomes more meaningful. Workers can share ideas, raise concerns, or offer solutions based on their firsthand experiences. This can lead to conversations that reveal unspoken risks or improve existing safety processes.
3. Keep It Short and Simple
Toolbox talks are meant to be short and sweet. Workers want to get on with their day, so aim for 10 to 15 minutes of focused discussion. Keep it brief but effective. Too much information at once can overwhelm them, so stick to the essentials and avoid overloading them.
4. Use Visuals and Demonstrations
Whenever possible, show rather than tell. Use real-life examples, props, or live demonstrations. If you’re talking about using PPE, demonstrate how to put it on correctly. If you’re discussing chemical handling, show workers the proper procedures step by step.
Visual aids make it easier to grasp the topic at hand and improve retention of key safety practices.
5. Document Everything
Don’t forget to document your toolbox talks. Write down the topics discussed, the date, and who attended. It not only serves as proof that you’re holding regular safety meetings (which can help during audits), but it also ensures that critical topics aren’t being missed over time.
While toolbox meetings are important, they’re just one part of a larger safety puzzle. They should be integrated into your company’s overall safety plan, which includes regular safety audits, hazard assessments, and incident reporting.
These quick discussions are great for keeping safety top-of-mind, but they need to be part of a continuous safety effort. For instance, after an accident or a near-miss, the following day’s toolbox meeting should focus on what went wrong and what can be done differently. This helps everyone learn from mistakes and ensures they don’t happen again.
Overcoming Challenges in Toolbox Meeting
Even though toolbox meetings are effective, some common challenges can pop up. Recognizing these and addressing them head-on ensures your meetings continue to add value:
1. Engagement Issues
Some workers might see toolbox talks as repetitive or unnecessary, especially if the same topics come up too often.
Solution: Switch things up. Rotate who leads the meeting to bring fresh perspectives and choose topics that align with the current tasks. Personal stories and real-life examples can also make the meeting feel more relevant.
2. Time Constraints
In busy industries, finding the time to stop and have a safety meeting can feel impossible.
Solution: Schedule toolbox talks at the start of the shift to minimize interruptions. Keep them short and to the point, ensuring they don’t delay work.
3. Lack of Preparation
Sometimes, toolbox meetings can feel rushed or unorganized.
Solution: Take time to plan ahead. Platforms like PEER offer customizable safety checklists and resources to help you prepare relevant, timely toolbox talks.
How to Measure the Success of Toolbox Meeting
It’s one thing to hold toolbox talks, but how do you know if they’re working? Here are a few ways to measure their impact:
- Track Incident Rates: Compare accident rates before and after implementing regular toolbox meetings. A reduction in incidents is a clear sign that the meetings are making a difference.
- Get Feedback from Workers: Ask workers for their input. Are they finding the talks helpful? What do they think could be improved? Regular feedback ensures the talks stay relevant and engaging.
- Review Safety Audits: Use toolbox talks to address any issues that pop up during safety audits. If you notice gaps or deficiencies, make sure your meetings cover those topics moving forward.
The Future of Safety and Toolbox Meetings
As industries evolve, so do the risks workers face. However, toolbox meetings will always remain an essential part of keeping workers safe. These short talks can adapt to the changing safety landscape, helping everyone stay aware of new hazards and best practices.
With the rise of digital safety platforms like PEER, companies now have more tools than ever to support safety initiatives. These platforms offer customizable checklists, real-time safety performance tracking, and tailored toolbox talk suggestions. By integrating these tools, companies can take their toolbox meetings to the next level, ensuring safety is at the forefront of daily operations.
Digitize Your Workplace Safety
Simolify your WSH processes to stay compliant and audit-ready.Conclusion
Toolbox meetings may seem small, but they pack a powerful punch. They’re a simple, efficient way to address safety concerns, keep workers informed, and prevent accidents. Whether you’re in construction, manufacturing, or the marine industry, toolbox meetings help create a culture where safety is prioritized, not just enforced.
By incorporating toolbox meetings into your daily routine and using platforms like PEER, you’re not only protecting your workers but also setting your business up for long-term success.